Introduction
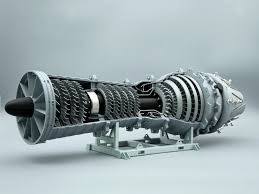
3D printed jet engines are transforming the aerospace industry by enabling rapid prototyping, cost-effective manufacturing, and lightweight design. Additive manufacturing, also known as 3D printing, allows engineers to create complex engine components with high precision, reducing material waste and production time. This cutting-edge technology is reshaping how jet engines are designed, built, and maintained.

How They Work
3D printed jet engines utilize additive manufacturing techniques such as selective laser melting (SLM), electron beam melting (EBM), and direct metal laser sintering (DMLS). These processes involve layering powdered metal materials, such as titanium or nickel alloys, and fusing them together using high-powered lasers or electron beams. The result is highly durable, lightweight components with intricate geometries that traditional manufacturing methods cannot achieve.
Uses of 3D Printed Jet Engines
- Commercial Aviation: Reduces manufacturing costs and improves fuel efficiency for passenger aircraft.
- Military and Defense: Enables rapid production of specialized jet engine components for fighter jets and drones.
- Space Exploration: Supports the development of lightweight, high-performance engines for spacecraft and satellites.
- Unmanned Aerial Vehicles (UAVs): Enhances the efficiency and longevity of drone propulsion systems.
- Prototyping and Research: Allows for quick testing and iteration of new jet engine designs.
Advantages
- Cost Reduction: Lowers material waste and reduces production costs compared to traditional manufacturing.
- Weight Efficiency: Produces lightweight components that improve fuel efficiency.
- Rapid Production: Shortens development time from months to weeks.
- Complex Designs: Enables the creation of intricate engine parts that would be impossible with conventional machining.
- Sustainability: Minimizes material waste, making manufacturing more environmentally friendly.
Disadvantages
- High Initial Investment: Requires expensive 3D printing equipment and expertise.
- Material Limitations: Not all aerospace-grade metals are suitable for additive manufacturing.
- Quality Control Challenges: Requires rigorous testing to ensure durability and performance meet industry standards.
- Limited Scalability: Mass production of large jet engines using 3D printing is still developing.
Future Scope
The future of 3D printed jet engines is promising, with ongoing advancements in material science, automation, and AI-driven design. Researchers are exploring new metal alloys and hybrid manufacturing techniques to enhance engine performance. As technology matures, 3D printing will play an even greater role in the production of next-generation, fuel-efficient jet engines, further driving innovation in the aerospace industry.
3D printed jet engines represent a paradigm shift in aerospace engineering, offering unprecedented efficiency and innovation. As additive manufacturing continues to evolve, it will redefine how jet engines are designed and produced for the modern aviation industry.
